14 Changes To Make Today To Reduce Injuries Tomorrow
Posted in Safety Tips
The reality is, it would have been easy to create a list of hundreds of things you could do today to reduce the chance of a injury happening at your facility. However, I wanted to provide you with a list of those items that are both easy to implement and have the potential to make an immediate impact.
With the above in mind, provided below are 14 suggestions that you can implement today.
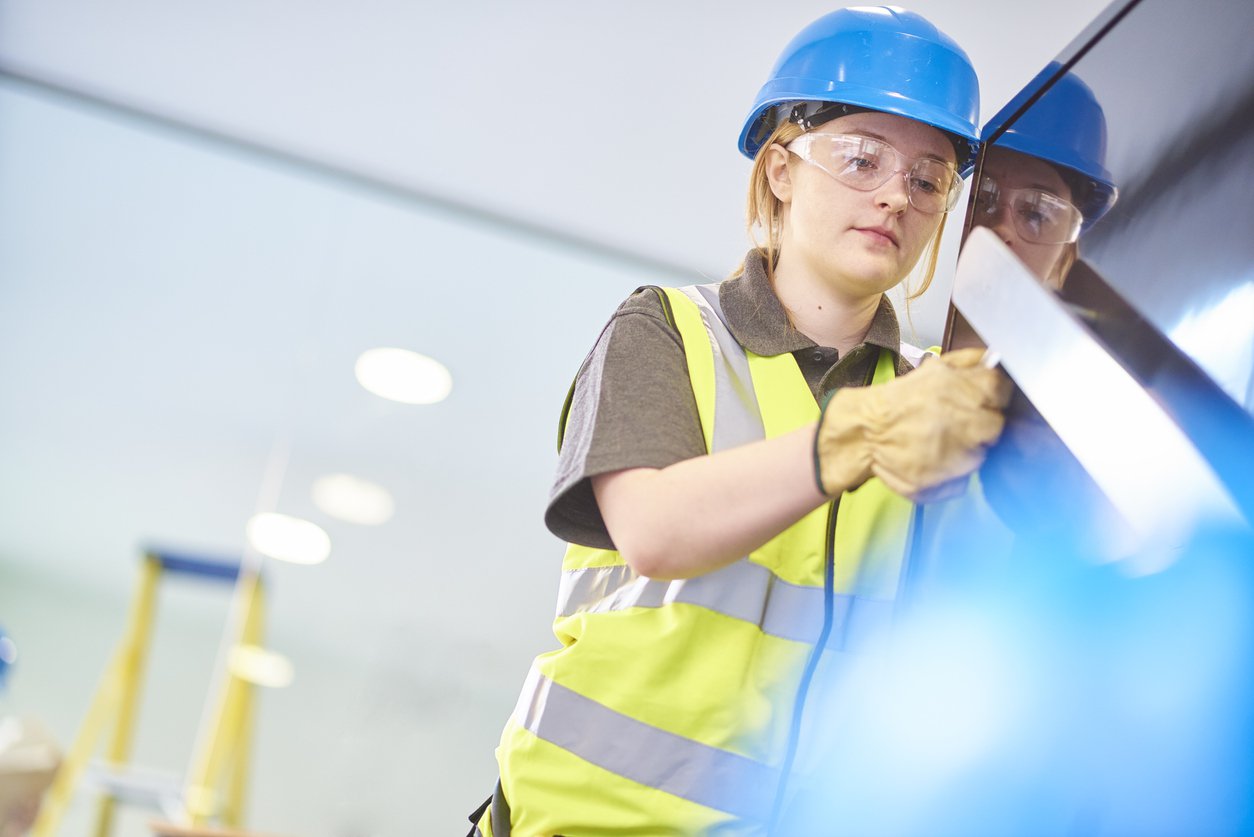
Eliminate Shortcuts: A safe work environment will not be achieved through shortcuts, deviations from proven safe procedures, or laziness. Make sure your employees are using the proper tools for the task at hand, make the time to use appropriate PPE and, perhaps most importantly, management leads by example. Remember, the time required to address an injury will far outweigh any time savings achieved from shortcuts.
Don't Become Blind To Workplace Hazards: How many times have you walked past an inherent risk that you are so used to seeing that it becomes invisible. These are accidents waiting to happen and you are turning a blind eye toward them. One easy way to identify these issues that "you no longer see" is to bring in an outside EHS expert to walk the facility with you. With a fresh eye and no bias, you can expect to receive a comprehensive list of action items to make your workplace safer.
Post Safety Guidelines: While it is impossible to assure every employee is compliant with all safety requirements all of the time, what is possible is to reinforce the behavior you expect. You can accomplish this through the use of visual reminders in the form of posted safety guideline. Not only will these postings remind employees of best practices, but they contribute to your overall program of creating a culture of safety.
Conduct Physicals Prior To Hiring: While a prospective employee may seem like the right candidate for the job on paper, when they actually have to perform, you may soon realize they don't have the experience or physical ability to perform the requirements of the position. When this occurs, it is a red flag for potential injury. This can be prevented by implementing a comprehensive screening process, including a pre-hiring physical.
Thoroughly Investigate Recurring Injuries and Near Misses: When similar types of injuries or near misses become a regular occurrence at your facility this is a sure sign that you have a flaw in your safety protocol. As the saying goes "Once is a mistake, twice is a habit." You need to correct bad habits to eliminate mistakes.
Provide The Proper PPE: As mentioned several times in this list, making sure your employees both have access to the proper PPE, AND use it, is essential to reducing workplace injuries. Take the time to teach (and if applicable, re-teach) employees how to properly use eye protection, hearing protection, gloves, hard hats, and other PPE needed for the tasks they perform.
Have Adequate Staffing Levels: More often than not, overtime hours are implemented because of low staffing levels. Overworked employees may suffer from exhaustion and cut corners to meet or exceed output. Hiring part-time or seasonal staff could help prevent accidents due to exhaustion.
Keep Your Workplace Clean and Free Of Clutter: Not only does poor housekeeping cause serious health and safety hazards, but it demonstrates to your employees that a culture of safety is not a priority. If you would be embarrassed to "showoff" your facility, that is a sign you have work to do.
Make Safety Training Mandatory: Train employees about workplace safety and how to identify hazards. Include workplace safety training as part of employee on boarding and offer refresher training on a regular basis. In addition to injury prevention training, consider including first-aid training so that your workforce can respond effectively if an accident does occur.
Conduct a Job Hazard Analysis For Every Task Performed In Your Facility: To assure all risks associated with a particular task have been reviewed and addressed, a job hazard analysis is essential. Not only will this process identify and then remove risks, it will also assure that employees are using the proper PPE for that task.
Lead By Example: Explain to supervisors and managers the importance of setting a good example and following all safety rules themselves, examples include wearing proper PPE and taking the same precautions as workers.
Encourage Feedback: Encourage employees to provide feedback on your safety program. Ask what they think is working and where there is room for improvement. Moreover, praise workers who identify and correct hazards, or who report problems they can't fix.
Look For Teachable Moments: When hazards are identified, do more than just correct them. Use them as learning experiences to help workers become more alert and more sensitive to potential dangers on the job.
The best way to protect your employees and help prevent accidents and injuries in your workplace is to take a holistic approach to workplace safety. This means ensuring your employees have the proper protective equipment and adequate training to perform their jobs, while also making sure your facility is compliant with federal and environmental regulations.
Arbill can provide the equipment and training you need while also offering safety and environmental site audits that provide a comprehensive review of your policies and procedures. Schedule a free consultation with an Arbill safety expert today and take the first step to ensuring your employees go home safely after every shift.
Have a Safe Day!